Technical Overview of Industrial Heat Pumps
- Melchior Krijgsman
- Mar 24
- 6 min read
Updated: 7 days ago
The Role of COP and Refrigerant Selection in Industrial Decarbonization š±š
Industrial heat pumps (IHPs) are critical for decarbonizing process heat in industrial sectors. This article presents a condensed yet high-level engineering analysis of their performance, system design, and working fluids, drawing on the latest technical literature and regulatory developments.
The Coefficient of Performance (COP) of a heat pump is defined as the ratio of heat delivered to work input, COP = Q_out / W. The theoretical upper bound is given by the Carnot equation:
COP_Carnot = T_out / (T_out ā T_in),
where temperatures are in Kelvin. In practice, industrial heat pumps operate at 65ā75% of the Carnot efficiency due to irreversibilities in compression, heat exchange, and fluid flow (check the article: kh.aquaenergyexpo.com). For instance, high-temperature systems capable of delivering steam at 215 °C achieve COP values around 2.7, while systems operating with smaller temperature lifts can reach COP values above 5 (check out the example of skyven.co). Temperature lift significantly affects performance. As the lift increases, the system moves further from reversible operation, and the COP decreases accordingly (check the article: kh.aquaenergyexpo.com).
To mitigate efficiency losses at high temperature lifts, engineering strategies such as multistage compression, vapor injection, economizers, and cascade cycles are commonly applied (check this example from heaten.com). Mechanical vapor recompression (MVR) systems, which use water or steam as the working fluid, are another effective approach, particularly in applications requiring high-grade heat above 150 °C. These systems bypass secondary refrigerants and leverage direct compression of vapor to achieve COPs between 2 and 4 under large temperature lifts (check out the example of skyven.co).
Designing efficient industrial heat pumps requires confronting a series of thermal and mechanical challenges. One major source of inefficiency is the approach temperature in heat exchangers, which increases the effective temperature lift the system must overcome, reducing efficiency (check the article: kh.aquaenergyexpo.com). Compressor inefficiencies, pressure drops, and thermal leakage further degrade system performance. To address these losses, advanced components such as magnetic-bearing centrifugal compressors and microchannel heat exchangers have been implemented in recent designs, enhancing performance and part-load modulation (check this example from heaten.com).
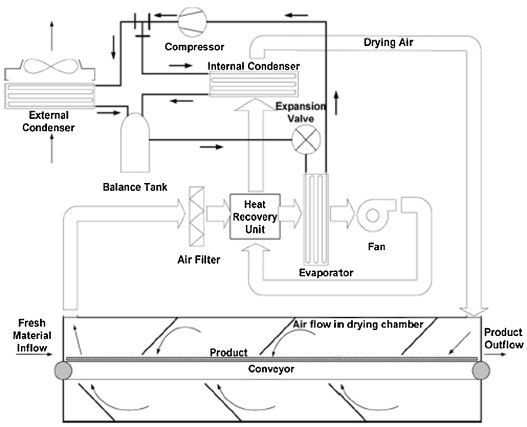
Material compatibility is also essential. Refrigerants used at high discharge temperatures must be chemically stable and compatible with lubricants and sealing materials. For instance, ammonia is incompatible with copper alloys, necessitating steel-based components. Projects using new HFOs at >130 °C have required custom oils and elastomers to ensure long-term stability (see article: heatpumpingtechnologies.org).
When retrofitting existing industrial processes, integration poses additional engineering challenges. Engineers must align heat pump output temperatures with process requirements while minimizing system disruption. In some cases, hybrid setups with auxiliary boilers are used to meet peak loads or ensure redundancy. Successful retrofits demand detailed engineering to manage temperature profiles, fluid dynamics, and control logic within existing thermal infrastructure (check it here: nrel.gov). A notable example involves a starch drying facility where a high-temperature heat pump was installed to displace gas burners. Integration required adjustments to flow, pressure, and sequencing but ultimately led to significant emission reductions (see article: heatpumpingtechnologies.org).
Refrigerant selection is central to both performance and environmental compliance. Key criteria include critical temperature, vapor density, and latent heat. For high-temperature applications, fluids like R1233zd(E) and R1336mzz(Z) are preferred due to their high critical points and thermodynamic stability (see article: mdpi.com). Ammonia (R717) remains popular for mid-temperature applications, while hydrocarbons such as propane (R290) are used under strict safety standards. COā (R744) is a viable natural refrigerant for systems operating in the transcritical regime below 100 °C (see article: mdpi.com).
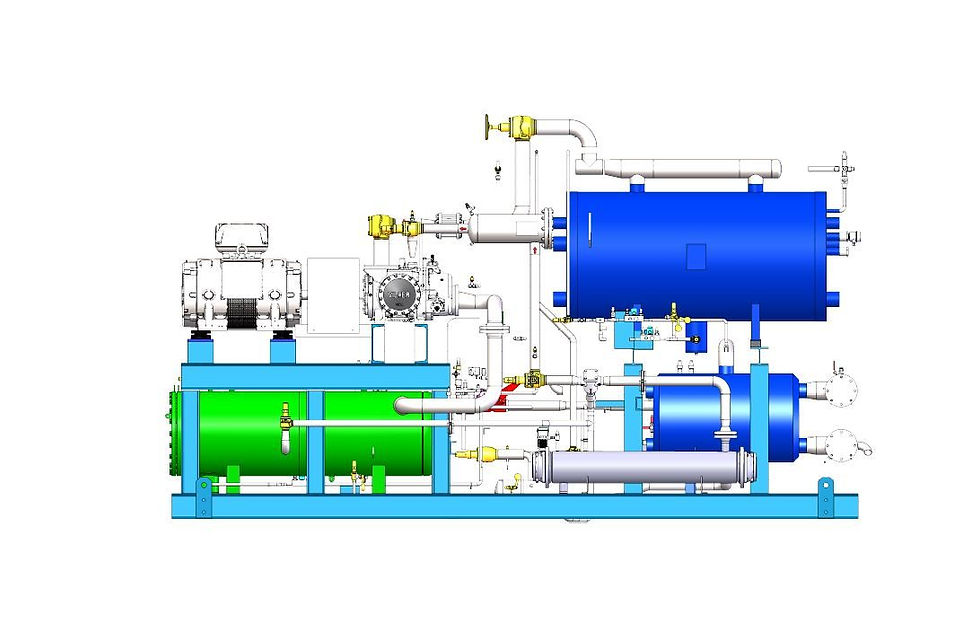
Refrigerant selection is further shaped by environmental regulations. The EU F-Gas Regulation prohibits high-GWP HFCs (GWP >150) in many new systems. As a result, refrigerants such as R134a (GWP ~1430) and R245fa (GWP ~1030) are being phased out in favor of low-GWP alternatives like R1234ze(E) (GWP ~7) and R1233zd(E) (GWP ~4ā7), which are permitted in new industrial equipment under EU law (for more details check this here: mdpi.com). Natural refrigerants such as ammonia (GWP 0), COā (GWP 1), and propane (GWP ~3) are exempt from these restrictions but require adherence to strict safety codes due to toxicity or flammability risks (for more details check this here: mdpi.com).Table 1 compares some common and emerging working fluids for industrial heat pumps, highlighting their GWPs and regulatory status under EU environmental policies:
Refrigerant | Type | GWP (100-yr)¹ | EU Regulatory Status (F-Gas/EU) |
R134aĀ (1,1,1,2-Tetrafluoroethane) | HFC | ~1430 | High GWPĀ ā Phased down under EU F-Gas quotas; banned in many new systems (GWP >150)ā |
R245faĀ (1,1,1,3,3-Pentafluoropropane) | HFC | ~1030 | High GWPĀ ā Being phased out; not viable in EU long-term (GWP >150)ā |
R1234ze(E)Ā (Trans-1,3,3,3-Tetrafluoropropene) | HFO | ~7 | Low GWPĀ ā F-Gas compliant (no restrictions); a key HFC replacement in new systemsā |
R1233zd(E)Ā (1-Chloro-3,3,3-trifluoropropene) | HCFO | ~4 to 7² | Ultra-Low GWPĀ ā Not restricted; allowed for new equipment (non-SFā fluorinated with negligible GWP).³ |
R717Ā (Ammonia NHā) | Natural (Inorganic) | ~0 | GWP=0Ā ā Not subject to F-Gas (not a fluorinated gas); usage governed by safety regulations (toxic/flammable). |
R744Ā (Carbon Dioxide COā) | Natural (Inorganic) | 1 | GWP=1Ā ā Not subject to F-Gas; no direct restrictions (ubiquitously allowed low climate impact). |
R290Ā (Propane CāHā) | Natural (Hydrocarbon) | ~3 | Very Low GWPĀ ā Not regulated by F-Gas; permitted in EU (with safety standards due to flammability)ā (check it here: mdpi.com). |
R1336mzz(Z)Ā (cis-1,1,1,4,4,4-Hexafluorobut-2-ene) | HFO | ~2 | Ultra-Low GWPĀ ā Not restricted; used in high-temperature systems (requires special design). |
GWP values are approximate 100-year values (COā = 1). EU regulations use IPCC AR4 values; for example, R134a GWP is 1430 and R1234ze(E) is 7 under that standard.² Reported GWP of R1233zd(E) varies by source (ā4.5 AR4, ā1 AR5).³ R1233zd(E) is an HCFO with a tiny ODP (~0.00024); it is allowed as a replacement for R123 under Montreal Protocol exemptions and is not banned by EU F-Gas due to its very low GWP.
As shown in the table,Ā EU environmental policy strongly disfavors high-GWP refrigerantsĀ in new industrial heat pumps. In fact, the EU is progressively banning the use of HFCs with GWP ā„150 in many types of stationary equipmentā (see article: mdpi.com). This has accelerated the transition to refrigerants like HFOs, HCFOs, and natural substances.Ā R134a and R245fa, once used in industrial systems, are essentially being replaced or designed out due to their GWP in the four-digits. R245fa, for instance, with GWP ~1000, is deemed unsuitable in the European context despite its favorable boiling pointā. On the other hand,Ā HFO-1234ze(E)Ā has a GWP in single digits and is a popular choice in new high-temp heat pumps (it can achieve ~120āÆĀ°C in some designs).Ā
Natural refrigerants (ammonia, COā, hydrocarbons) haveĀ inherent environmental advantagesĀ ā zero or near-zero GWP ā and thus face no looming bans under climate regulations. Ammonia and hydrocarbons are exempt from F-Gas limitations, and COā, being the baseline, is obviously exempt. This regulatory freedom makes them attractive for sustainability. However, their technical challengesĀ must be managed. Ammonia is toxic and mildly flammable (ISO safety class B2L), requiring careful handling, leak detection, and often exclusion from occupied spaces. Industry has decades of experience with ammonia, so standards are well-established, and it remains a top choice for large systems where safety can be controlled (e.g. in a dedicated machinery room).Ā Propane and other hydrocarbons (A3: highly flammable)Ā carry a risk of fire or explosion, which limits charge sizes and necessitates explosion-proof equipment. Despite this, hydrocarbon heat pumps are feasible and increasingly common in smaller to medium installations; in an industrial setting, they might be suitable in outdoor or well-ventilated locations with small charge or as secondary loop systems. COā operates at very high pressures and can have lower efficiency in high-temperature applications, which somewhat limits its use to specific niches. Still, its benign environmental profile and non-toxicity make it appealwherever its thermodynamic limitations can be tolerated (e.g. heating from 20āÆĀ°C to 80āÆĀ°C with transcritical COā is quite effective, and such systems are on the market).
Looking ahead, the search for theĀ optimal low-GWP refrigerantĀ for high-temperature heat pumps continues.Ā Hydrofluoroolefins (HFOs)Ā and Hydrochlorofluoroolefins (HCFOs)Ā are leading the way for now, as they combine much lower GWP with manageable operating pressures. They are consideredĀ ādrop-inā replacements for many banned HFCsĀ under EU rulesā (see the article: mdpi.com), albeit some are mildly flammable (A2L). The mild flammability of HFOs like R1234ze(E) means systems must adhere to charge limits or ventilation requirements per standards (EN378, ISO 5149), but these are not insurmountable for industrial setups. Another promising avenue is the development of newĀ blendsĀ that achieve non-flammability while keeping GWP low; for example, adding a small amount of a high-GWP, non-flammable HFC to an HFO (as in refrigerant R515B, a blend of R1234ze and R227ea) can yield an A1 refrigerant with moderate GWP ā though care must be taken, as some blends still end up with GWP above the 150 threshold and thus are only interim solutions.
In conclusion, the performance of industrial heat pumps is governed by the interplay between thermodynamic efficiency, system integration, and refrigerant properties. Optimizing COP requires a combination of staged compression, internal heat recovery, and precise matching of working fluids to process conditions. Environmental regulations are accelerating the transition to low-GWP refrigerants, further shaping the engineering landscape of next-generation heat pump technologies.
Comments