Engineering High-Temperature Industrial Heat Pumps: Design and Integration Challenges
- Melchior Krijgsman
- Apr 2
- 6 min read
Updated: 7 days ago
Modern high-temperature industrial heat pumps (IHPs) are emerging as a game-changing technology to decarbonize process heat in industries like chemicals, pulp & paper, and food processing. These systems can deliver heat at much higher temperatures (often 100–150 °C or more) than conventional heat pumps, in capacities of multiple megawatts (check the articles here: coolingpost.com, mckinsey.com). However, achieving such performance reliably is no small feat. This article delves into the thermodynamic challenges and component-level engineering hurdles in high-temperature heat pump design – from working fluid selection and compressor design to heat exchangers and controls. It also examines pre-engineering integration issues (retrofit complexity, system dynamics, material durability) and illustrates solutions with real industrial examples. Finally, we discuss how Entropic’s engineering approach addresses these challenges to ensure industrial reliability and scalability.
Thermodynamic Challenges at High Output Temperatures
Industrial heat pumps operate on the same vapor-compression cycle principles as smaller units, but pushing output temperatures into the 120–150 °C range introduces significant thermodynamic challenges. A key issue is the declining coefficient of performance (COP) as the temperature lift increases. The larger the gap between the heat source and the desired hot output, the more work the compressor must do per unit of heat delivered – yielding lower efficiency. Carnot’s law sets an upper limit: for example, an ideal heat pump raising heat from 60 °C to 120 °C has a COP of ~7, but at 150 °C output that ideal COP falls below 5. Real-world systems operate at a fraction of Carnot efficiency (often 40–60%), so actual COPs might drop from ~3–4 at moderate lifts to near 2 at extreme lifts. In practice, early high-temperature heat pumps around 120 °C achieved COPs on the order of 2.5–3.5 (for more data check here: nrel.gov), meaning careful design is needed to keep energy savings attractive.
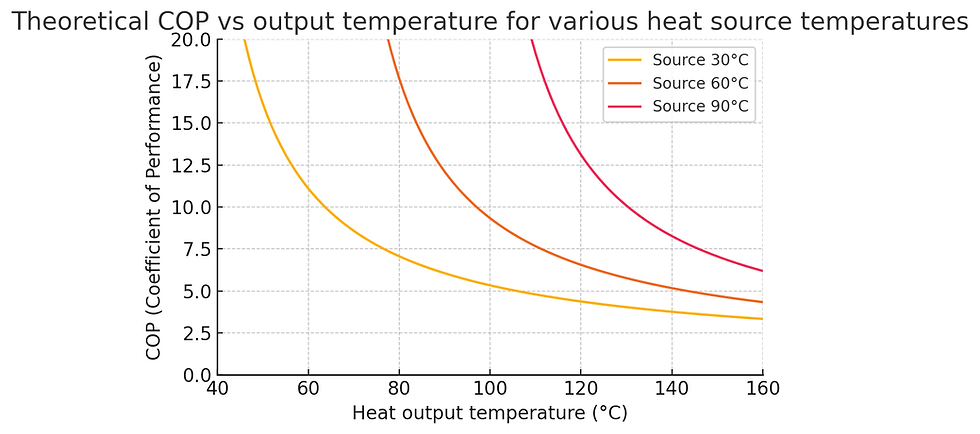
To mitigate the efficiency-drop at high temperatures, engineers employ strategies like two-stage compression, cascaded refrigerant cycles, and internal heat recovery. Multi-stage compression with interstage cooling reduces the work per stage and avoids excessively high discharge temperatures, improving overall COP. In some cases, cascade heat pump systems use two different refrigerant circuits in series – for instance, an ammonia-based cycle providing intermediate heating (e.g. up to ~80 °C) which feeds a second cycle using a high-boiling refrigerant to reach 150 °C. This approach was demonstrated in a Norwegian food plant: an ammonia heat pump first upgraded waste heat from ~21 °C to 82 °C, then a pentane-based heat pump boosted it to 150 °C steam for a cooker (check the article: spirit-heat.eu). Such designs keep each stage within a reasonable temperature lift for better efficiency. Thermodynamically, maintaining smaller temperature differences in each heat exchanger (approach temperature) and using techniques like economizers or vapor injection can also help sustain a higher COP at these elevated temperatures (check the article here: solarthermalworld.org). The challenge is to balance complexity with efficiency gains – every additional stage or heat exchanger introduces cost and control complexity, so they must be justified by performance benefits.
Compressor and Component Design Challenges
Achieving high temperatures reliably places severe demands on the heat pump’s components, especially the compressor and heat exchangers. The compressor must generate much higher-pressure ratios than a standard heat pump, often in excess of 10:1. For example, condensing at 120 °C with ammonia requires roughly 50–60 bar discharge pressure and a 150 °C pentane cycle might operate around 25–30 bar on the high side (for more data check here: heatpumpingtechnologies.org). High-temperature heat pumps require specialized industrial compressors—typically screw or reciprocating types—for their ability to handle high pressures and staged compression. Screw compressors suit large systems with smooth operation, while reciprocating ones achieve high-pressure ratios in compact setups. Centrifugal compressors are used for light gases but struggle with off-design conditions. A key challenge is managing high discharge temperatures, which can degrade oil and materials; this is addressed via intercooling, high-temp lubricants, and advanced oil systems like Mayekawa’s cooled, degassed oil loop in its 150 °C cascade system.

Oil injection is used to cool and seal the screw compressor, but the oil leaving the hot discharge is actively recovered and cooled to prevent thermal degradation (for more details check here: spirit-heat.eu). Such design tweaks are critical to ensure the compressor’s longevity when dealing with 150 °C outputs. In other cases, two-stage compression with an oil separator and cooler between stages is employed – after the first stage, oil and some heat are removed, reducing the temperature entering the second stage.
The choice of compressor technology also depends on the working fluid. For example, ammonia compressors at >50 bar often require steel alloys (as ammonia is incompatible with copper and has high pressure) and typically use reciprocating or screw compressors with limited speed to manage discharge heat (for more details heck here: heatpumpingtechnologies.org). High-temperature heat pumps face significant hardware challenges due to extreme pressures, temperatures, and phase changes. Compressors must tolerate over 120 bar, often requiring oil-free or carefully cooled and filtered lubrication systems, while heat exchangers must handle thermal stress and material degradation. Expansion valves and cascade systems demand precise control, making advanced instrumentation and control systems—sometimes AI-assisted—crucial to maintaining safe, stable operation under dynamic conditions.
Pre-Engineering Integration and Retrofit Issues
Integrating a high-temperature heat pump into an existing industrial process requires careful pre-engineering and smart system integration, as it must work around existing infrastructure. A key challenge is matching waste heat sources (like exhaust or condenser water) with suitable heat demands, often identified through pinch analysis; if temperatures are too low, more advanced setups like cascade systems may be needed.
Retrofit complexity arises from the need to tie into existing utilities. Consider a case in the chemical industry: BASF’s Ludwigshafen site (a huge chemical complex) is studying a multi-megawatt heat pump to use waste heat from their cooling water network to produce process steam (Check the successful example by man-es.com). The pre-engineering had to examine how the heat pump would interface with the cooling water circuit (without upsetting its primary cooling function) and how the generated steam would be introduced into the steam headers. Often, existing boilers or steam systems remain in place for backup, so the heat pump must be integrated in parallel. This requires control coordination: e.g. when the heat pump is running, the boiler should modulate down, and vice versa, to maintain steady steam pressure. The system dynamics can be challenging – industrial processes may have batch operations causing swings in heat demand. A heat pump doesn’t ramp heat output as instantaneously as a gas burner; thus, engineers might include a buffer storage (thermal accumulator) or stage multiple smaller compressors that can turn on/off to match load steps (for more details check the articles here: enerin.no, sciencedirect.com). Ensuring that the heat pump’s response is compatible with process requirements (for example, not letting a pasteurization line cool down too much before the heat pump catches up) is part of the integration challenge.
Another integration issue is operating fluid compatibility and safety in an industrial setting. If the chosen refrigerant is flammable (like a hydrocarbon) or toxic (ammonia), the heat pump unit may need to be placed in a secure area or even outdoors, with secondary heat transfer loops conveying heat to the process indirectly. This adds complexity (an extra heat exchanger and pump) but can be necessary to satisfy safety codes. For example, in the sugar plant installation by GEA, the system uses pentane (flammable) in a self-contained circuit to heat water/steam, which then delivers heat to the sugar process (check the article here: coolingpost.com). All pentane-containing components are housed in a safety-rated enclosure, with operators mainly interacting with steam, reducing risk. Integration challenges include connecting high-temperature systems to older infrastructure, requiring pre-engineering checks for durability and maintenance planning—often with isolation valves or redundancy. Examples include a Czech paper mill and a Norwegian prawn plant, both requiring careful retrofitting alongside existing systems (for more details check the articles here: coolingpost.com, spirit-heat.eu). The engineers had to add the ammonia/pentane heat pumps, connect the ammonia cycle to the existing refrigeration condensers, and feed the pentane cycle’s output into the steam cooker line – all while preserving the operation of the original systems. These cases underline that each industrial application is unique, and a successful project demands a holistic view of the plant’s energy flows, control logic, and safety requirements from the earliest design stages.
Entropic’s Approach to High-Temp Heat Pump Challenges
At Entropic, we tackle industrial heat pump integration through detailed pre-engineering and smart design. Using advanced tools, including AI simulations and pinch analysis, we map waste heat and process demands to identify ideal integration points, reducing retrofit complexity. Our team then tailors the system—selecting optimal systems and cycles based on application needs, safety, and cost—drawing on a proprietary database and deep knowledge of component performance.
We ensure system reliability by working with top equipment vendors and adhering to industrial standards, carefully sizing compressors, heat exchangers, and piping. Designs include redundancies like dual compressors and robust control systems tested with dynamic simulations, enabling real-time response to load or utility shifts. We also integrate IoT monitoring for predictive maintenance and long-term performance optimization.
Beyond design, Entropic supports clients with operations training and procedures, ensuring teams are comfortable with the new tech. By combining engineering expertise with on-the-ground know-how, we de-risk heat pump projects and help industries—from chemicals to food—decarbonize efficiently, without sacrificing uptime or safety.
Commentaires