Top Industrial Heat Pump Manufacturers: 4 examples of Success
- Melchior Krijgsman
- Mar 17
- 13 min read
Updated: 7 days ago
Industrial heat pumps have emerged as a powerful weapon in the fight for energy efficiency and sustainability. By capturing waste heat or ambient energy and “upcycling” it to useful high temperatures, these systems dramatically reduce the need for fossil-fueled boilers. In fact, industrial heat pumps (IHPs) are 3–8 times as energy-efficient as traditional heating methods, slashing energy use, costs, and emissions (see article: aceee.org). Studies show they can cut CO₂ emissions by over 80% when replacing fossil heat sources ehpa.org. No wonder they’re hailed as a crucial technology for industrial decarbonization. Approximately 37% of all industrial process heat in Europe is below 200 °C – a range well suited for heat pump solutions (see article: ehpa.org). By tapping into this opportunity, manufacturers are helping make factories greener and more circular in their energy use.

Today, industrial heat pumps are enabling industries from food processing to chemicals to save energy and reduce their carbon footprint. But who are the companies driving this revolution? Below we highlight some of the top industrial heat pump manufacturers – from well-known engineering giants to innovative startups – and how they’re pushing the boundaries of efficiency and heat recovery.
Why Industrial Heat Pumps Matter
Unlike household heat pumps that keep homes cozy, industrial-scale heat pumps tackle the heating needs of factories, district heating networks, and large facilities. They often replace or supplement boilers by taking a source of heat (for example, waste heat from an oven or cooling system, or heat from air, water or geothermal sources) and boosting its temperature via a refrigeration cycle. This process delivers usable heat for processes or space heating while consuming far less energy than direct fuel combustion or electric resistance heating. The result is a double win: companies dramatically cut their energy consumption and greenhouse emissions while often saving on operating costs in the long run (see article: aceee.org).
Crucially, industrial heat pumps allow manufacturers to recover heat that would otherwise be wasted, making processes more efficient. They can also run on renewable electricity, meaning the provided heat can be nearly carbon-free. As one research coordinator noted, “Heat pumps are a future-proof technology for process heat – we can reduce CO₂ emissions by up to over 80% and increase energy efficiency” with their adoption (see article: ehpa.org).
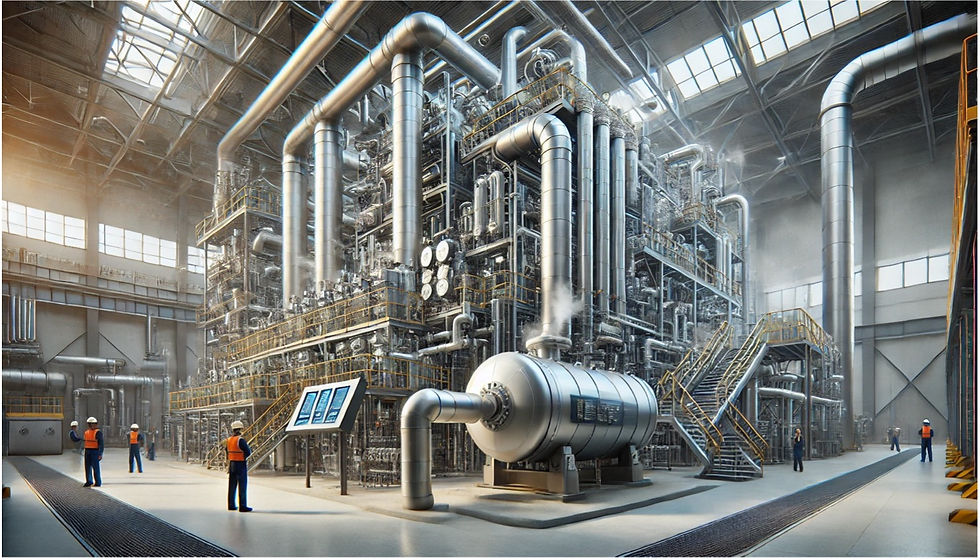
With global and local climate targets tightening, many companies are turning to heat pump technology to decarbonize heat, which accounts for a large share of industrial energy use and CO₂ emissions.
Government and industry initiatives are accelerating this trend. For instance, the U.S. Department of Energy’s Industrial Heat Shot program is fostering breakthroughs toward 85% lower-emission industrial heating by 2035 (see article: aceee.org)
In Europe and Asia, numerous pilot projects and policies are boosting confidence in high-temperature heat pumps. The stage is set for wider adoption – and the leading manufacturers below are at the forefront of making industrial heat pumps bigger, better, and more accessible.
Leading Industrial Heat Pump Manufacturers
Who are the key players supplying industry with these game-changing heat pump systems? Here’s our ranked list (in no strict order) of top industrial heat pump manufacturers, each with their strengths, innovations, and market impact. We’ve included 4 established leaders of the field to serve them as model to describe the current dynamic landscape:
1. Johnson Controls (Sabroe)
Johnson Controls – through its Sabroe product line – is a pioneer in industrial heat pumps. Sabroe has been building high-capacity and high-temperature heat pumps since as far back as 1982, and today it boasts a leading portfolio of industrial solutions focused on energy efficiency and reliable performance (see article: sabroe.com). This long legacy means Johnson Controls’ heat pumps are found in countless factories, cold storage facilities, and district heating plants worldwide.

Strengths & Innovations: Johnson Controls/Sabroe specializes in using natural refrigerants (like ammonia) in their large heat pump systems, aligning with sustainability goals. Their designs are modular and flexible, making it possible to capture waste heat at multiple temperature levels with optimal efficiency (see article: sabroe.com). All units come with advanced control systems (e.g. the UniSAB III) to ensure peak performance and uptime. Sabroe’s lineup ranges from high-capacity reciprocating heat pumps (for big heating duties with a small footprint) to screw-compressor heat pumps tailored for faster, cost-effective installation (see article: sabroe.com). Notably, Sabroe developed the HyePAC high-temperature heat pump, a hybrid absorption/compression system that can heat water up to 120 °C using a clever blend of technologies – an attractive solution for dairies, food processors, and even pharma labs needing hot water or steam (see article: sabroe.com). This spirit of innovation – combining proven refrigeration tech with novel approaches – keeps Johnson Controls at the cutting edge of industrial heat pumping.
Market Impact: As a global HVAC&R giant, Johnson Controls has a vast reach. Its industrial heat pumps (often sold under the Sabroe and YORK brands) help heavy industries and large buildings phase out fossil-fuel boilers. By providing turnkey cooling-and-heating solutions, they’ve helped many clients achieve sustainability targets and energy cost savings. With decades of installations, Johnson Controls has proven that industrial heat pumps are a reliable workhorse – not just a futuristic concept. It continues to refine the technology, recently integrating its heat pumps with smart automation and monitoring (via the OpenBlue platform) to maximize efficiency. Few companies can match Johnson Controls’ combination of experience, breadth of product range, and global service network in the industrial heat pump arena.
2. GEA
GEA is another heavyweight in the industrial heat pump market, known for its engineering excellence in refrigeration and heat recovery systems. Headquartered in Germany, GEA has leveraged its expertise in compressors and thermal technology to offer some of the most efficient and robust industrial heat pumps available. The company emphasizes solutions that use natural refrigerants like ammonia for eco-friendliness (see article: gea.com).
Strengths & Innovations: GEA’s heat pumps are celebrated for their high efficiency and compact, innovative designs. A prime example is the GEA RedAstrum series – a standard ammonia screw compressor heat pump line designed to meet the growing demand for efficient industrial heating. The RedAstrum is known for its wide capacity and temperature range, achieved with high-end components and a sophisticated, space-saving design (see article: gea.com). GEA also offers customized heat pump systems for cases that exceed standard limits, ensuring that virtually any industrial heating demand (from moderate process heat to district heating supply) can be met (see article: gea.com). They even combine chillers and heat pumps in hybrid configurations (like the GEA Blu-Red Fusion) to simultaneously deliver refrigeration and high-grade heat, squeezing every drop of usefulness out of input energy.
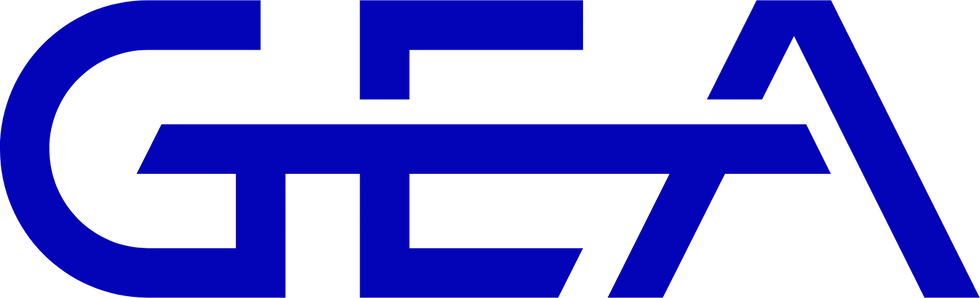
A key innovation is GEA’s focus on modularity and quick payback. Their systems are built to integrate into existing processes with minimal disruption and tend to have short amortization periods thanks to energy savings (see article: gea.com). By prioritizing the use of ammonia and other low-GWP refrigerants, GEA ensures compliance with environmental regulations and future-proofs their installations. They also provide advanced control systems and remote monitoring to keep performance optimal.
Market Impact: With a presence in numerous industries (food & beverage, dairy, chemicals, etc.), GEA has helped many facilities transition towards greener operations. The company often highlights that heat accounts for over half of global final energy consumption, mostly from fossil fuels – and thus sees its mission to “heat to cool” the planet as vital (see article: gea.com). GEA’s industrial heat pumps have been adopted in projects ranging from large dairy plants (reusing waste heat from cooling for pasteurization) to district heating networks looking to replace coal/gas. By delivering reliable products with strong performance, GEA has built a reputation as a go-to supplier for industries aiming to improve energy efficiency. Their active role in advocacy and research (they frequently participate in pilot projects and publish case studies) further solidifies their impact on advancing heat pump technology worldwide.
3. Siemens Energy
When it comes to scaling up heat pump technology to utility levels, Siemens Energy stands out. This engineering titan (a spin-off of Siemens focusing on energy solutions) has leveraged its deep expertise in power plants and turbomachinery to develop large-scale industrial heat pumps suited for district heating and heavy industrial processes. Siemens Energy proudly positions itself as one of the leading manufacturers of industrial heat pumps, with technology proven over decades (see article: siemens-energy.com).
Strengths & Innovations: Siemens Energy’s heat pump offerings are all about going big – in temperature, capacity, and reliability. Their systems can deliver forward temperatures up to 150 °C and on the order of tens of megawatts of thermal output (see article: siemens-energy.com). For example, they offer heat pump configurations rated around 70 MWₜₕcapacity for ~150 °C output – enough to supply a small town’s heating needs from a single unit! (see article: siemens-energy.com). These high-performance figures are backed by real operational history: Siemens Energy notes it delivered around 50 large heat pump units as early as the mid-1980s, accumulating over 6 million operating hours of experience since then (see article: siemens-energy.com). This track record lends enormous credibility to their technology.
A hallmark of Siemens Energy’s approach is integrating heat pumps into the broader energy system. Their vision is to use excess renewable electricity (e.g., wind or solar power during off-peak times) to run heat pumps that feed district heating grids or industrial processes, effectively converting green electricity into useful heat (see article: siemens-energy.com). This not only cuts emissions but also helps balance the grid. Siemens offers complete solutions including the heat pump units (often based on large-scale compressors and expanders), auxiliary equipment, and controls. They also focus on safe, modern refrigerants with negligible environmental impact, ensuring their systems meet strict safety and environmental standards (see article: siemens-energy.com).

Market Impact: Siemens Energy has made headlines with some of the largest heat pump projects in Europe. For instance, they supplied a high-temperature heat pump to the Potsdamer Platz cooling plant in Berlin, and more recently, a 20 MW “river heat” pump in Mannheim, Germany that draws warmth from Rhine river water to heat about 3,500 households (see article: siemens-energy.com). Such projects demonstrate that city-scale heating via heat pumps is no longer theoretical – it’s happening now, enabled by companies like Siemens. By bringing its industrial clout and engineering rigor into the heat pump sector, Siemens Energy is accelerating the energy transition in the heating domain. Their influence also extends through advocacy; Siemens experts frequently speak on the urgency of electrifying heat (pointing out that 40% of the world’s energy-related emissions come from heat and urging immediate action to change that) (see article: ehpa.org). In summary, Siemens Energy marries huge capacity with proven durability, making it a top choice for large industries and municipalities aiming to decarbonize heat.
4. Turboden (A Mitsubishi Heavy Industries Company)
Turboden, a subsidiary of Mitsubishi Heavy Industries (MHI), is a prominent player in the field of industrial heat pump solutions. Leveraging its expertise in Organic Rankine Cycle (ORC) systems, Turboden has expanded its portfolio to include large-scale heat pumps (LHPs), addressing the growing demand for efficient and sustainable heating solutions in industrial processes and district heating networks. (see Turboden’s website https://turboden.com)
Strengths & Innovations
High-Temperature Capabilities: Turboden's LHPs are engineered to deliver thermal outputs starting from 5 MWₜₕ per unit, with output temperatures exceeding 200°C, including steam generation. This makes them suitable for energy-intensive sectors such as refineries, petrochemicals, chemical and pharmaceutical industries, food processing, and pulp and paper. (For a more detailed explanation: https://turboden.com)
Advanced Compressor Technology: The company utilizes in-house developed centrifugal compressors, designed for continuous operation with reduced maintenance. These compressors offer enhanced flexibility for optimal part-load operation and quick process adaptation, ensuring high reliability and availability. (For specifications: https://turboden.com+1Wisconsin Industrial Energy Group+1)
Mechanical Vapor Recompression (MVR): Turboden integrates MVR systems, acting as open-cycle water heat pumps, to increase both the temperature and pressure of water streams, generating steam at specific conditions needed for industrial processes. This technology is particularly applicable in sectors like distillation processes in the petrochemical industry and crystallization processes in the food and beverage industry. (For a more detailed explanation on the functioning https://turboden.com+1HPT - Heat Pumping Technologies+1)
Sustainability Focus: By capturing and repurposing low-grade heat sources, Turboden's LHPs contribute to reducing CO₂ emissions and enhancing energy efficiency, aligning with global efforts to mitigate climate change. (see the article: https://turboden.com)

Market Impact
Decarbonizing Industrial Processes: Turboden's LHPs have been instrumental in projects aimed at decarbonizing industrial steam demands. For instance, an innovative heat upgrade system, based on the integration of Turboden's LHP and a mechanical vapor compressor, exploits low-grade heat (ranging between 10°C and 20°C) to produce 12 MWₜₕ of superheated steam at 170°C, utilized in the paper production process. (Check also the Mitsubishi Heavy Industry website: Mitsubishi Heavy Industries, Ltd.+1https://turboden.com+1https://turboden.com+1https://turboden.com+1)
District Heating Integration: In the steel industry, Turboden's LHPs have been deployed to recover waste heat from steelmaking processes and upgrade it for district heating purposes. A notable example is the installation at ORI Martin steelworks in Italy, where a 6 MWₜₕ LHP exploits waste heat to serve the local district heating network, providing pressurized water at 120°C to approximately 3,500 households. https://turboden.com+1YouTube+1
Global Reach: As part of the MHI group, Turboden has expanded its global footprint, delivering over 450 plants in 52 countries, thereby demonstrating its capability to provide reliable and clean energy systems worldwide. (For more specifications check here: Spectra by MHI+1https://turboden.com+1)
Collaborative Synergies: The partnership between Turboden and MHI combines Turboden's expertise in ORC systems and LHPs with MHI's engineering and manufacturing capabilities in centrifugal compressors and turbomachinery. This synergy enhances the efficiency and reliability of Turboden's heat pump solutions, contributing significantly to industrial decarbonization efforts. (see article: https://turboden.com+1Mitsubishi Heavy Industries, Ltd.+1)
Educational Outreach: Turboden actively engages in knowledge dissemination by organizing events such as 'Heat Electrification, ready technological decarbonisation solutions for industries and utilities', focusing on LHP technology and market developments, thereby fostering the transition to clean heat. (see article: https://turboden.com)
Through continuous innovation and strategic collaborations, Turboden plays a pivotal role in advancing industrial heat pump technologies, supporting the global transition towards sustainable and efficient energy systems.
(For a visual overview of Turboden's impact on decarbonizing the steel industry through large heat pumps, you can watch the following video: https://youtu.be/QAb99mRBGQ0)
Future Trends and Innovations
Industrial heat pump technology is advancing rapidly, and the coming years promise even more exciting developments. One key trend is the push toward higher temperatures and larger capacities. Where 120–150 °C was once the ceiling, we now see systems delivering 180–200 °C, and prototypes reaching 280 °C (see article: aceee.org). This will open the door for heat pumps to penetrate industries like chemicals, paper, and metals processing, where very high heat is required. Research and trials (such as the EU’s SPIRIT and PUSH2HEAT projects) are focused on breaking the remaining technical barriers and proving these solutions at scale
(see article: ehpa.org)
Another clear trend is the shift to ultra-low-GWP refrigerants and even non-traditional working fluids. Manufacturers are increasingly favoring natural refrigerants — ammonia, CO₂, hydrocarbons — or new synthetic blends (HFOs) that have minimal climate impact. This not only reduces the environmental footprint of the heat pumps themselves but also future-proofs them against evolving refrigerant regulations. For example, GEA has shown that ammonia and hydrocarbons can be used effectively in high-capacity systems, and companies like Siemens Energy explicitly design their heat pumps for “safe and non-hazardous” refrigerants from the start (see article: siemens-energy.com). We may also see more hybrid systems combining heat pumps with other technologies: e.g., vapor-compression heat pumps paired with absorption modules (to extend temperature range), or heat pump + electric boiler combos for flexibility.
Improving efficiency further is always on the agenda. The best industrial heat pumps today often reach coefficients of performance (COPs) of 3–6 (meaning 1 unit of electricity yields 3–6 units of heat). Future systems may squeeze this even higher through better heat exchangers (like 3D-printed designs or nano-coated surfaces for heat transfer), more advanced compression technology (magnetic-bearing compressors, two-stage compression for big temperature lifts), and smarter integration. Speaking of integration: expect to see heat pumps playing a role in integrated energy systems – for instance, acting as a buffer for the electrical grid. An industrial site might use a heat pump as a “thermal battery,” storing excess renewable power as heat in water tanks during the day, then using it at night. This kind of synergy amplifies the sustainability impact beyond just the factory in which the heat pump sits.
Digitalization and AI are also up-and-coming trends. Many heat pump makers are deploying cloud-based monitoring and AI-driven control optimizations. These can predict and adjust operation for maximum efficiency or detect maintenance needs before a failure. As heat pumps become mission-critical infrastructure for heat supply, such reliability enhancements are crucial.
Finally, the market itself is set to expand. As awareness grows that industrial heat pumps can deliver on their promises, more companies will jump in, both as manufacturers and users. Analysts predict double-digit growth in industrial heat pump adoption in the next decade, fueled by corporate net-zero pledges and supportive policies. This competition will likely drive costs down, making projects even more economically attractive. We’re already seeing more suppliers from around the globe (Europe, Asia, North America) enter the field, each bringing their own twist or specialty.
In summary, the future of industrial heat pumps looks bright – and hot! We’re moving toward a world where burning fuels for medium-temperature heat could become as antiquated as burning kerosene for lighting. The companies leading today’s market are continuously innovating, and new players are bringing fresh ideas. All of this means better, more efficient, and more sustainable heat solutions for factories and cities.
Conclusion: Heating Up the Conversation
Industrial heat pumps are no longer a niche or experimental technology – they are here now, scaling up, and reshaping how industries think about energy. From giants like Johnson Controls and Siemens Energy, to specialized experts like GEA and Turboden, manufacturers highlighted above are delivering real-world solutions that save energy and cut emissions. They’re proving that even the most heat-intensive processes can be made cleaner and more efficient. And as we’ve discussed, the pace of innovation is only accelerating, promising even greater capabilities in the near future.
Choosing the right heat pump partner or solution depends on the specific needs – whether it’s ultra-high temperature steam, a turn-key package for a food plant, or a massive district heating installation. The market leaders we’ve ranked have all demonstrated unique strengths, be it in technology, reliability, or scope of offerings. Together, they are driving competition and improvements across the board, which ultimately benefits all industrial heat pump users.
Now, we’d love to hear from you. Are you considering an industrial heat pump for your facility, or have you worked with any of the manufacturers mentioned? Which company or technology do you think is most exciting in this space? Perhaps there’s a promising manufacturer we didn’t include or a breakthrough development on the horizon – let us know! The conversation around industrial heat pumps is heating up (in the best way possible), and the more we share knowledge and experiences, the faster we can all move toward a more energy-efficient, sustainable future. Feel free to drop a comment or reach out with your thoughts and questions on our LinkedIn page direct messages, or also by commenting one of our posts. Let’s keep the momentum going and continue exploring how to turn waste heat into gold for industry.
Comments